Hợp lý hóa chi phí sản xuất, cải tiến chất lượng sản phẩm với công cụ TPM

(VietQ.vn) - Thực hiện TPM giúp doanh nghiệp tối ưu hóa hiệu suất hoạt động, loại bỏ sự cố, sai sót của máy móc thiết bị thông qua việc tự bảo dưỡng máy móc trong quá trình sản xuất hàng ngày. Điều này sẽ giúp doanh nghiệp hợp lý hóa chi phí sản xuất, cải tiến chất lượng sản phẩm và dịch vụ, nâng cao khả năng cạnh tranh trên thị trường.
Sự kiện: Chuyên đề: NÂNG CAO NĂNG SUẤT CHẤT LƯỢNG
Yêu cầu an toàn giàn giáo xây dựng theo TCVN 13662:2023
Góp ý tiêu chuẩn quốc gia tín hiệu phát thanh số mặt đất DAB+
Lựa chọn vật liệu và thiết kế cột chống thép kiểu ống lồng theo TCVN 13661:2023 đảm bảo độ bền cao
TPM là phương pháp quản lý được áp dụng đầu tiên tại Nhật Bản. Cốt lõi của TPM là nhằm tối đa hóa hiệu suất thiết bị, nâng cao năng suất hệ thống bảo trì được thực hiện trong suốt vòng đời thiết bị, đồng thời nâng cao ý thức và sự hài lòng với công việc của người lao động.
Thực hiện TPM giúp doanh nghiệp tối ưu hóa hiệu suất hoạt động, loại bỏ sự cố, sai sót của máy móc thiết bị thông qua việc tự bảo dưỡng máy móc trong quá trình sản xuất hàng ngày. Điều này sẽ giúp doanh nghiệp hợp lý hóa chi phí sản xuất, cải tiến chất lượng sản phẩm và dịch vụ, nâng cao khả năng cạnh tranh trên thị trường.
Với TPM, mọi người cùng hợp lực và tương tác với nhau để nâng cao hiệu suất hoạt động thiết bị một cách hiệu quả nhất. TPM hướng nhiều vào phần cứng của hệ thống sản xuất trong công ty nên các đối tượng thích hợp áp dụng là tổ chức/doanh nghiệp có hoạt động sản xuất, trong đó, phần máy móc thiết bị tham gia đóng góp lớn cho việc tạo ra cũng như đóng vai trò quan trọng quyết định chất lượng sản phẩm.
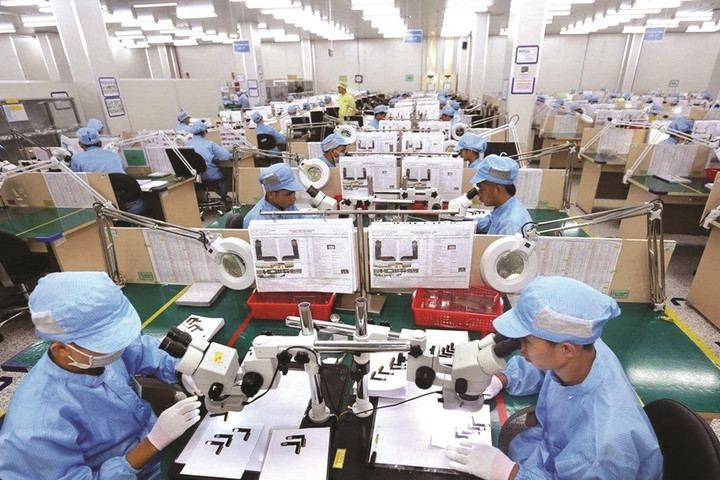
10 mục tiêu của TPM là: (1) Đạt được 3 Không: Không sản phẩm lỗi, Không sự cố, Không tai nạn; (2) Lôi cuốn toàn thể người lao động vào các hoạt động nhóm để bảo dưỡng tự giác và cải tiến thiết bị; (3) Nâng cao năng suất chất lượng và Chỉ số hiệu suất thiết bị toàn bộ (OEE); (4) Giảm thiểu chi phí sản xuất sinh ra do máy hỏng, máy dừng; (5) Giao hàng đúng hạn 100%; (6) Không để khách hàng phàn nàn; (7) Không để xảy ra tai nạn; (8) Khuyến khích các sáng kiến cải tiến của người lao động; (9) Chia sẻ kinh nghiệm; (10) Cải thiện môi trường làm việc.
Theo các chuyên gia, có 5 bước cơ bản để thực hiện kế hoạch bảo trì năng xuất toàn diện và lợi ích của TPM.
Bước 1 - Xác định khu vực thí điểm
Khi chọn thiết bị thí điểm, có thể chọn bắt đầu với một máy đơn giản, không quan trọng đối với sản xuất hoặc ngược lại, với máy là nguyên nhân gây ra tắc nghẽn hoặc rất quan trọng.
Xét về những người cùng nỗ lực thực hiện thí điểm TPM nên tập trung càng nhiều nhân viên càng tốt. Điều đó sẽ giúp xây dựng động lực và khi những lợi ích của chương trình TPM được hiện thực hóa, đảm bảo nỗ lực không làm doanh nghiệp thất vọng.
Bước 2 - Trả thiết bị về tình trạng cơ bản
Khi khu vực thí điểm đã được xác định, đó là lúc kết hợp TPM vào 5S và bảo trì tự quản. Ý tưởng ở đây là tất cả những người tham gia TPM nên liên tục khôi phục thiết bị trở lại tình trạng cơ bản bằng cách sử dụng các hoạt động được nêu trong nền tảng 5S.
Một khi điều này được thiết lập như hiện trạng, các nhà điều hành và nhân viên bảo trì nên bắt đầu chương trình bảo trì tự quản của họ, bao gồm thiết bị làm sạch trong khi kiểm tra sự hư hỏng hoặc bất thường, xác định và loại bỏ các yếu tố góp phần làm hỏng và thiết lập tiêu chuẩn để làm sạch, kiểm tra và bôi trơn một tài sản đúng cách.
Bước 3 - Chỉ số hiệu suất thiết bị toàn bộ
Chỉ số hiệu suất thiết bị toàn bộ (OEE) hoặc hiệu quả của thiết bị tổng thể, đo lường mức độ sẵn có của thiết bị, cách thức hoạt động và loại chất lượng mà nó tạo ra.
Đo lường điều này thường xuyên sẽ cung cấp cho doanh nghiệp một chỉ số tuyệt vời về việc chương trình TPM của doanh nghiệp có hoạt động như kế hoạch hay không. Điều này cũng sẽ cung cấp cho doanh nghiệp xác nhận dựa trên dữ liệu về việc các nỗ lực loại bỏ thời gian chết của doanh nghiệp có hoạt động hay không và sau đó theo dõi hiệu quả các nỗ lực của doanh nghiệp theo thời gian.
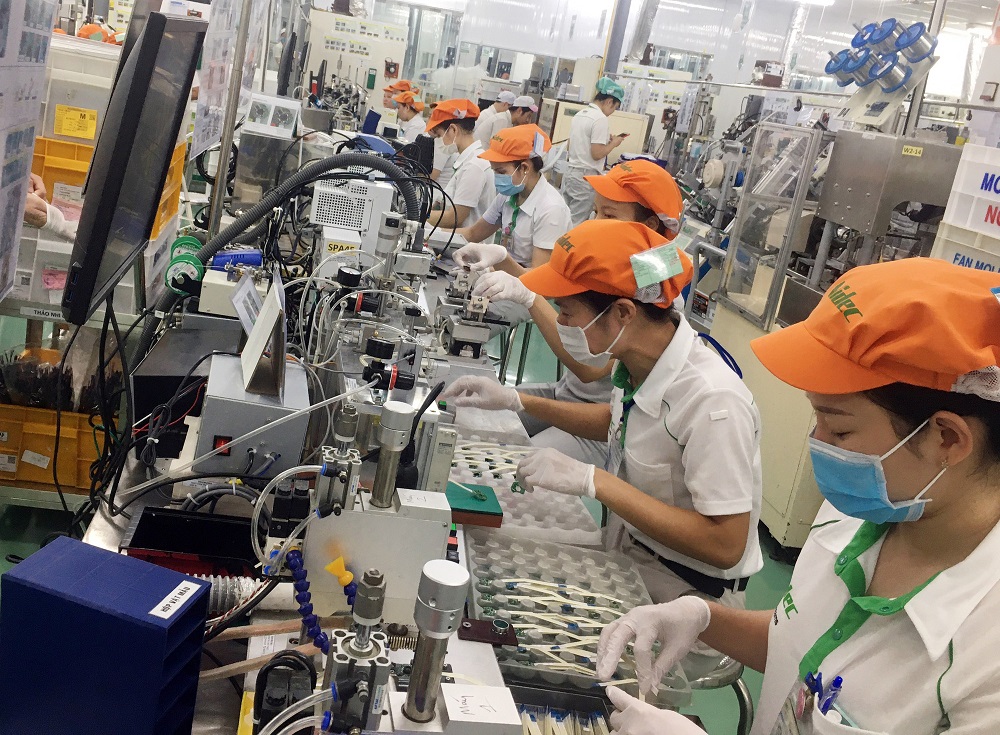
Bước 4 - giảm tổn thất lớn
Bước này được thực hiện bằng cách tập trung cải tiến trụ cột để triển khai TPM hiệu quả. Khi OEE đã được thiết lập, điều quan trọng là phải tập hợp một nhóm chức năng chéo có thể xem dữ liệu OEE đã được tạo ra và xác định các lý do chính cho các tổn thất đã xảy ra.
Sau khi phân tích nguyên nhân gốc rễ đã được tiến hành, các biện pháp có thể được thực hiện để loại bỏ những tổn thất này nếu có thể. Việc tiếp tục sử dụng phép đo OEE sẽ xác minh xem các nỗ lực cải tiến tập trung có hoạt động như kế hoạch hay không.
Bước 5 - Thực hiện bảo trì theo kế hoạch
Giai đoạn cuối cùng của việc triển khai TPM hiệu quả là lập kế hoạch và lên lịch các hoạt động bảo trì.
Không phải mọi khía cạnh của bảo trì năng suất toàn diện đều có thể đưa vào vận hành cùng lúc. Doanh nghiệp sẽ thành công hơn khi thực hiện từng bước một.
Hà My